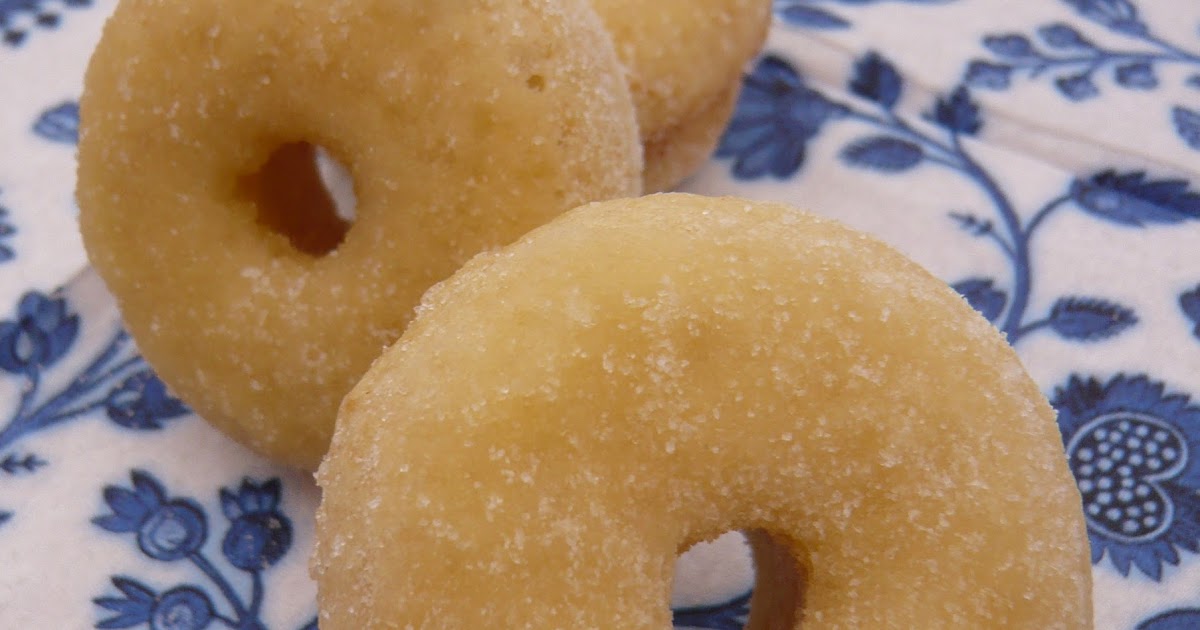
Doughnut Dilemma: Unraveling the Supply Woes Plaguing Dunkin’ Stores
Introduction
Dunkin’, the iconic coffee and doughnut chain, has recently been facing a puzzling supply crisis that has left shelves empty and customers frustrated. This article delves into the complexities of this doughnut dilemma, examining the causes, consequences, and potential solutions to this unexpected disruption.
Delays and Shortages
In recent weeks, Dunkin’ stores across the United States have reported significant delays and shortages of key ingredients, including coffee, doughnuts, and other breakfast items. The company’s supply chain has been severely disrupted, leading to long wait times, cancellations, and a decline in customer satisfaction.
Multiple Factors
The supply chain issues faced by Dunkin’ are attributed to a combination of factors:
- Labor Shortages: Like many industries, the food service sector is struggling to find and retain workers, particularly in transportation and distribution.
- Supply Chain Disruptions: The ongoing pandemic and global economic challenges have impacted supply chains worldwide, leading to delays and increased costs.
- Increased Demand: As the economy recovers, demand for Dunkin’ products has increased, putting a strain on the company’s supply chain.
- Operational Challenges: Internal operational issues, such as inefficient inventory management or production delays, may also be contributing to the shortages.
Customer Impact
The supply woes have had a significant impact on Dunkin’ customers. Disgruntled customers have taken to social media to express their frustration and disappointment, while some stores have been forced to adjust their hours or close temporarily.
Financial Implications
The supply chain disruptions are also having financial consequences for Dunkin’. Lost sales due to shortages, increased transportation costs, and potential penalties for missed deliveries are all contributing to the company’s operating expenses.
Seeking Solutions
Dunkin’ is actively working to address the supply chain issues. The company has implemented several measures, including:
- Increasing Supplier Capacity: Partnering with suppliers to increase production and shorten lead times.
- Re-evaluating Inventory Management: Implementing stricter inventory controls to prevent stockouts.
- Investing in Technology: Exploring automation and digital tools to improve supply chain visibility and coordination.
li
Improving Transportation Efficiency: Optimizing routes and leveraging technology to streamline logistics.
Industry Perspectives
The supply chain disruptions faced by Dunkin’ are not unique to the company. Other food and beverage businesses have experienced similar challenges. Experts in the industry believe that the labor shortage, coupled with the global supply chain crisis, will continue to pose significant obstacles.
Conclusion
The doughnut dilemma faced by Dunkin’ is a complex issue with multiple causes. While the company is taking steps to address the supply chain disruptions, it is uncertain when the situation will fully resolve. In the meantime, customers may continue to experience delays or shortages of their favorite Dunkin’ treats. The broader implications of these supply chain issues extend beyond Dunkin’; they serve as a reminder of the fragility and interconnectedness of today’s global supply chains.
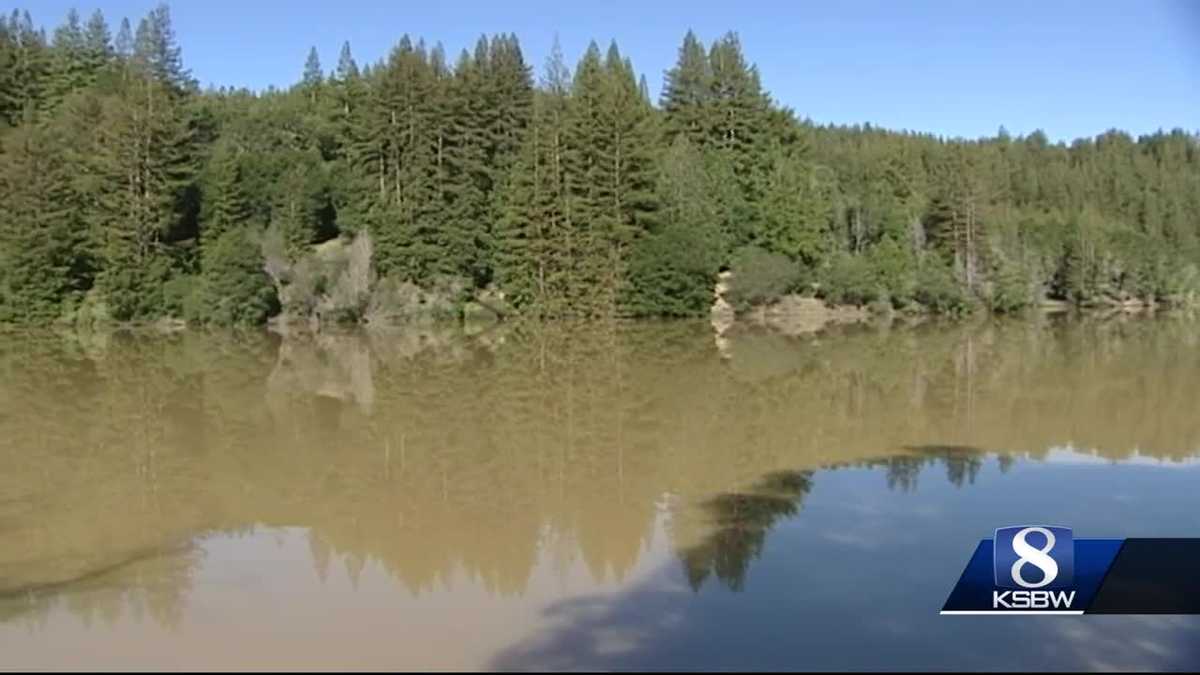